anko
Well-known member
As part of my OBDII adventure, I am trying to create a dashboard showing the behaviour of the E-motors. What I have so far is this:
First column is obviously the name of the parameter. Second column is value for front motor, third is rear motor, and fourth is second and third column added together.
Rows are:
- TRQ Req Nm: Torque in Nm Request(ed by ECU?), I disabled this for the time being, as this parameter requires one extra separate OBDII request per motor, which makes sweep time to long.
- TRQ Nm: Torque delivered
- RPM: spinning speed
- Current 1: Is a parameter in the motor ECU that expresses current in Amps
- Current 2: Is a second parameter in the motor ECU that expresses current in Amps
- Current +: Me trying to add current 1 and current 2, trying to see if I could match battery output.
- Current -: Me trying to subtract current 2 from current 1, trying to see if I could match battery output.
- Charge: Fourth column shows battery output in Amps.
- Power Out: Torque in Nm * RPM / 9.5488 / 1000 to yield kW
- Power+: Attempt to determine power consumed by E-motor via (Current 1 + Current 2) * battery total voltage
- Power-: Attempt to determine power consumed by E-motor via (Current 1 - Current 2) * battery total voltage
- Charge: Fourth column is kW output from battery, third column is Wh output from battery per km
- Speed: speed in km/h
- Batt Volt: battery total voltage
Most numbers are negative, because I took the photo during regen breaking. Doesn't really matter.
What I try to do is match power output from the battery to power consumption by the E-motors (this is all in EV mode).
Also, I try to compare power consumption by E-motors to power output by E-motors.
- need to finish this post later, as the family needs me -
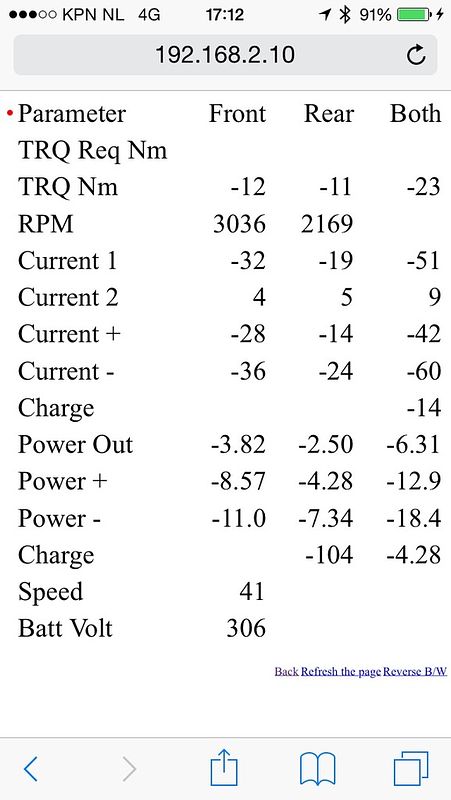
First column is obviously the name of the parameter. Second column is value for front motor, third is rear motor, and fourth is second and third column added together.
Rows are:
- TRQ Req Nm: Torque in Nm Request(ed by ECU?), I disabled this for the time being, as this parameter requires one extra separate OBDII request per motor, which makes sweep time to long.
- TRQ Nm: Torque delivered
- RPM: spinning speed
- Current 1: Is a parameter in the motor ECU that expresses current in Amps
- Current 2: Is a second parameter in the motor ECU that expresses current in Amps
- Current +: Me trying to add current 1 and current 2, trying to see if I could match battery output.
- Current -: Me trying to subtract current 2 from current 1, trying to see if I could match battery output.
- Charge: Fourth column shows battery output in Amps.
- Power Out: Torque in Nm * RPM / 9.5488 / 1000 to yield kW
- Power+: Attempt to determine power consumed by E-motor via (Current 1 + Current 2) * battery total voltage
- Power-: Attempt to determine power consumed by E-motor via (Current 1 - Current 2) * battery total voltage
- Charge: Fourth column is kW output from battery, third column is Wh output from battery per km
- Speed: speed in km/h
- Batt Volt: battery total voltage
Most numbers are negative, because I took the photo during regen breaking. Doesn't really matter.
What I try to do is match power output from the battery to power consumption by the E-motors (this is all in EV mode).
Also, I try to compare power consumption by E-motors to power output by E-motors.
- need to finish this post later, as the family needs me -